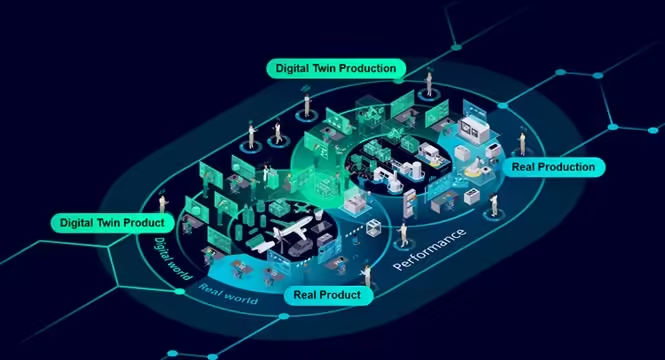
Digital Twins
Digital twins represent a revolutionary concept in the realm of industrial automation, where the physical and digital worlds converge. A digital twin is essentially a virtual replica of a physical asset, process, or system that captures and simulates its behavior in real time. This interplay between the physical objects and their digital counterparts allows for enhanced monitoring, analysis, and optimization of operations, leading to increased efficiency and productivity.
The importance of digital twins in industrial automation cannot be overstated. They provide a framework for real-time data integration, enabling businesses to analyze and visualize asset performance comprehensively. By utilizing advanced sensor technology and the Internet of Things (IoT), physical assets produce vast amounts of data that can be synchronized with their digital twins. This integration allows organizations to leverage predictive analytics, identify potential failures before they occur, and drive better decision-making through data-driven insights.
At the core of digital twin technology is the synchronization of physical and digital systems. This involves capturing not just static data but also dynamic information that reflects current operating conditions. Digital twins utilize algorithms and simulation models to provide stakeholders with a clear understanding of how a physical asset will behave under various scenarios. Thus, they facilitate proactive maintenance strategies, contribute to the safe operation of machinery, and even influence product design and development.
Overall, the concept of digital twins represents a significant advancement in how industries can manage and optimize their assets. As organizations increasingly adopt such technologies, the applications of digital twins will continue to expand, shaping the future of industrial automation and contributing to smarter, more interconnected operations.
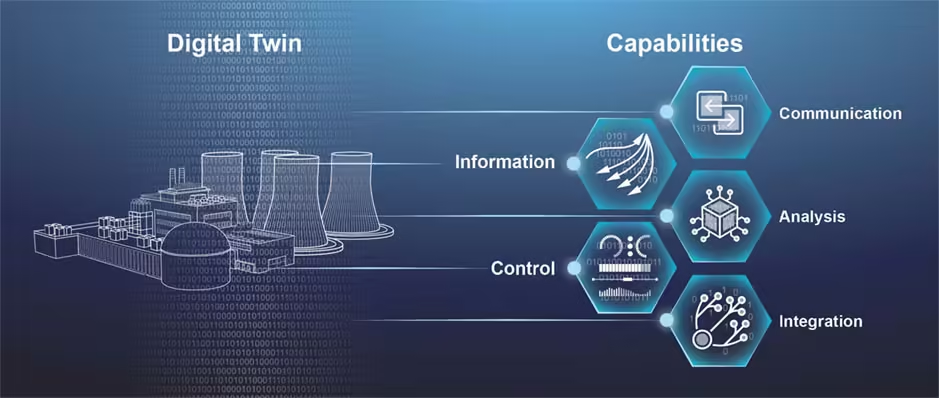
The Evolution of Industrial Automation
The landscape of industrial automation has undergone a remarkable transformation since its inception. Traditionally, manufacturing processes relied heavily on manual labor and basic mechanization, where mechanical devices were used to perform repetitive tasks. As industries aimed for greater efficiency, the advent of programmable logic controllers (PLCs) in the late 20th century marked a significant milestone. PLCs enabled manufacturers to automate processes with greater precision and flexibility, setting the stage for the developments that would follow.
However, the integration of automation technologies was not without its challenges. Early automation systems often operated in isolation, leading to inefficiencies and limited data visibility. As industries expanded, the need for interconnected systems became ever more pressing. The rise of information technology brought about new possibilities, yet it also highlighted issues such as data silos and communication barriers among different automation components.
The introduction of advanced technologies, such as the Internet of Things (IoT), signified the next phase in the evolution of industrial automation. IoT enabled devices to communicate and share data seamlessly, paving the way for smarter manufacturing environments. Nevertheless, these technological advancements also raised concerns regarding data security and standardization across platforms, challenging industries to adapt rapidly.
In this context, digital twins emerged as a revolutionary concept. By creating virtual representations of physical assets, digital twins provide real-time insights into system performance and health. This innovation significantly enhances process efficiency and productivity, addressing many of the historical challenges faced by manufacturers. The utilization of digital twins facilitates better predictive maintenance, allowing businesses to minimize downtime and optimize resource allocation. As industrial automation continues to evolve, the significance of digital twins cannot be overstated, reinforcing their role as a transformative force in the sector.
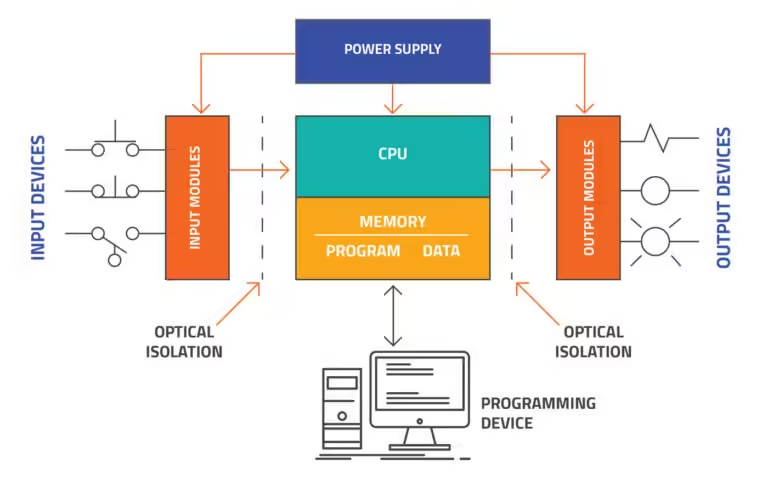
Components of Digital Twin Technology
Digital twin technology is a sophisticated framework composed of various interdependent components that collectively enable the creation and maintenance of accurate digital representations of physical systems. At the core of a digital twin system are sensors, which are responsible for collecting real-time data from the physical asset. These sensors can measure various parameters, such as temperature, pressure, and vibration, providing an essential data stream that reflects the operational status and performance of the physical system.
Data analytics is another crucial component, as it processes the vast amounts of data generated by the sensors. By utilizing advanced analytical techniques, such as statistical analysis and predictive modeling, stakeholders can gain insights into system behavior and performance patterns. This analysis not only aids in understanding historical performance but also supports proactive decision-making by forecasting potential failures or inefficiencies.
Moreover, the integration of machine learning algorithms plays a significant role in enhancing the functionality of digital twins. These algorithms can learn from historical data and constantly refine their predictive capabilities, allowing for continuous improvement in performance predictions. As the digital twin evolves over time, it generates more accurate models, helping operators make informed operational decisions.
Furthermore, the essence of digital twin technology is bolstered by the integration of the Internet of Things (IoT). IoT devices facilitate seamless communication between the physical and digital realms, ensuring that the digital twin remains updated with the latest data. This interconnectedness enables real-time monitoring and control, creating a dynamic feedback loop that enhances operational efficiency and responsiveness.
Together, these components—sensors, data analytics, machine learning, and IoT integration—form the backbone of digital twin technology. They work in unison to create a comprehensive, real-time digital representation of physical assets, paving the way for transformative improvements in industrial automation.
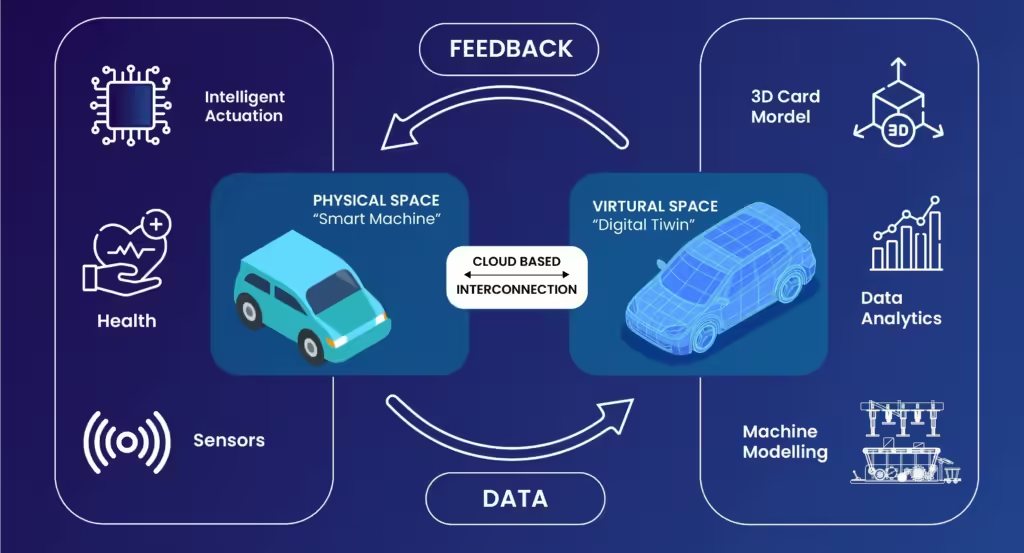
Applications of Digital Twins in Industry
Manufacturing and Production
In manufacturing, digital twins are used to monitor machinery, optimize production lines, and ensure quality control. They provide insights that help improve productivity, reduce defects, and streamline operations.
- Predictive Quality Control: Digital twins can simulate production processes, identify potential quality issues, and allow manufacturers to address them before products reach the market.
Energy and Utilities
Digital twins assist in optimizing energy consumption, monitoring infrastructure, and ensuring the reliability of power generation assets. In renewable energy, they can simulate wind farms or solar power plants to maximize energy output.
- Grid Optimization: Utility companies use digital twins to manage and optimize power grids, ensuring stable electricity distribution and preventing outages through predictive maintenance.
Oil and Gas
Oil and gas companies rely on digital twins for asset management, predictive maintenance, and environmental monitoring. They help in modeling complex equipment, ensuring safe drilling operations, and enhancing extraction efficiency.
- Pipeline Monitoring: Digital twins of pipelines help detect leaks or weaknesses, enabling timely maintenance and reducing the risk of spills.
Transportation and Logistics
Digital twins in logistics optimize supply chain operations, improve asset utilization, and enhance route planning. They can model warehouses, simulate storage configurations, and track vehicle fleets.
- Fleet Management: In logistics, digital twins monitor fleet performance, track vehicle health, and optimize routes to ensure timely delivery and reduced fuel consumption.
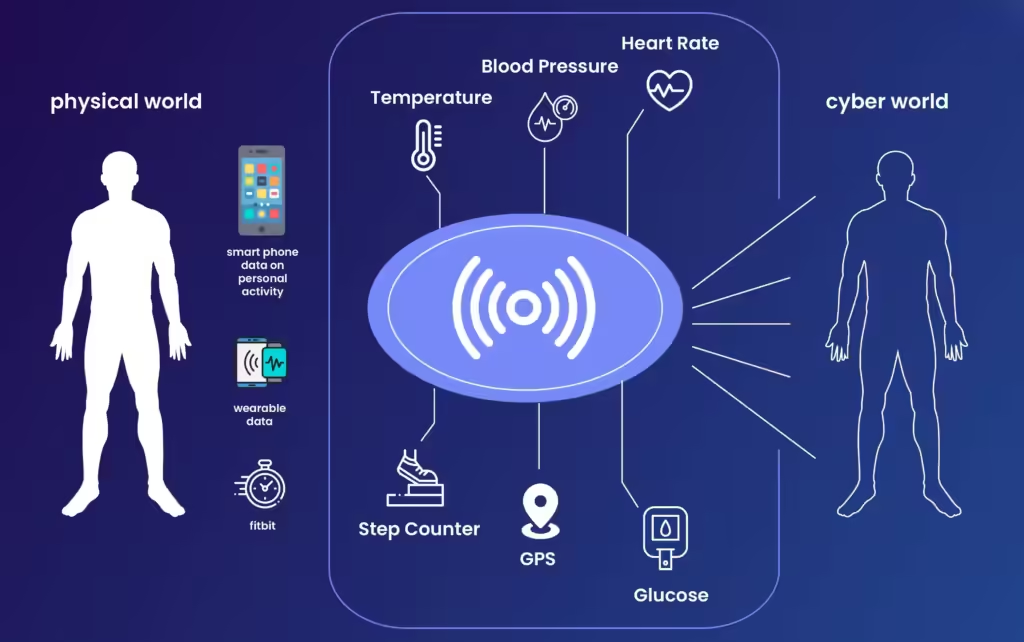
Benefits of Implementing Digital Twins
The integration of digital twins into industrial automation offers numerous benefits that can significantly enhance operational efficiency and overall productivity. One of the most notable advantages is the reduction of downtime. By creating accurate virtual representations of physical assets, industries can monitor equipment health in real-time. This proactive approach allows for timely maintenance and repairs, which helps to minimize disruptions in production schedules and ultimately leads to considerable cost savings.
Real-Time Monitoring and Optimization
Digital twins enable real-time monitoring by integrating data from IoT sensors attached to physical assets. This continuous stream of data provides insight into machinery performance, environmental conditions, and production status. Operators can track anomalies, optimize processes, and address inefficiencies as they arise, ensuring smoother, more efficient operations.
- Example: In the manufacturing sector, digital twins monitor assembly lines, identifying bottlenecks or delays in real time, enabling operators to make adjustments on the fly to maintain productivity.
Predictive Maintenance and Reduced Downtime
Predictive maintenance, supported by digital twins, is transforming industrial maintenance practices. By monitoring asset health and predicting failures, digital twins help prevent costly downtime and extend asset lifespans.
- Example: A digital twin for a turbine can alert operators to potential failures before they occur, based on wear-and-tear data from sensors. This helps schedule timely maintenance, thus reducing unplanned downtime and optimizing resource use.
Enhanced Decision-Making and Data-Driven Insights
Digital twins provide comprehensive data that can be analyzed for better decision-making. They help operators understand patterns, improve forecasting, and plan more efficiently.
- Example: In the oil and gas industry, digital twins model drilling operations and provide data to enhance decision-making, improve safety, and increase extraction efficiency.
Virtual Testing and Simulation
Digital twins allow for risk-free testing and simulation. Companies can simulate changes, test new workflows, or train employees in a virtual environment without impacting physical systems.
- Example: Before launching a new production line, manufacturers can test the process in a digital twin environment, minimizing the risks associated with new equipment, configurations, or workflows.
Furthermore, digital twins enable enhanced decision-making through advanced data visualization techniques. They aggregate and present real-time data from various sources, allowing stakeholders to analyze and interpret complex information easily. This capability empowers managers and engineers to make informed decisions based on up-to-date insights, thereby improving both short-term and long-term strategic planning.
Another significant benefit of implementing digital twin technology is the improvement of product design and testing processes. By simulating various scenarios and environments digitally, organizations can identify potential design flaws early in the development phase. This capability fosters innovation, reduces time-to-market, and enables companies to deliver high-quality products that meet market demands more effectively.
Agility in responding to market changes is also enhanced through the application of digital twins. These virtual models provide businesses with the ability to simulate different market conditions and consumer behaviors, allowing them to devise strategies and adapt quickly. This responsiveness not only helps companies maintain a competitive edge but also promotes resilience in an ever-evolving industrial landscape.
In conclusion, the adoption of digital twins in industrial automation presents a myriad of advantages, including reduced downtime, enhanced decision-making, improved product design and testing, and greater agility in market response. As industries increasingly embrace this technology, the overall impact on operational excellence is expected to be profound.
How Digital Twins Enhance Automation and Robotics
Autonomous Operations and Self-Optimization
Digital twins enable autonomous decision-making in industrial automation by continuously feeding real-time data into AI systems, which then make adjustments automatically. In autonomous manufacturing, for example, robots can rely on data from digital twins to adapt their actions based on environmental or operational changes.
- Example: Autonomous robots in a factory can use digital twins to navigate around obstacles, recalibrate tasks, or switch tools based on data insights, reducing the need for human intervention.
Robotic Process Simulation
In robotics, digital twins are used to simulate robot movements and actions, allowing developers to test different configurations and workflows. This can improve efficiency, reduce setup times, and enhance safety by allowing processes to be validated before deployment.
- Example: Automotive manufacturers use digital twins to simulate robotic assembly lines, reducing time and resources spent on configuring robotic arms and reducing the margin of error in complex tasks.
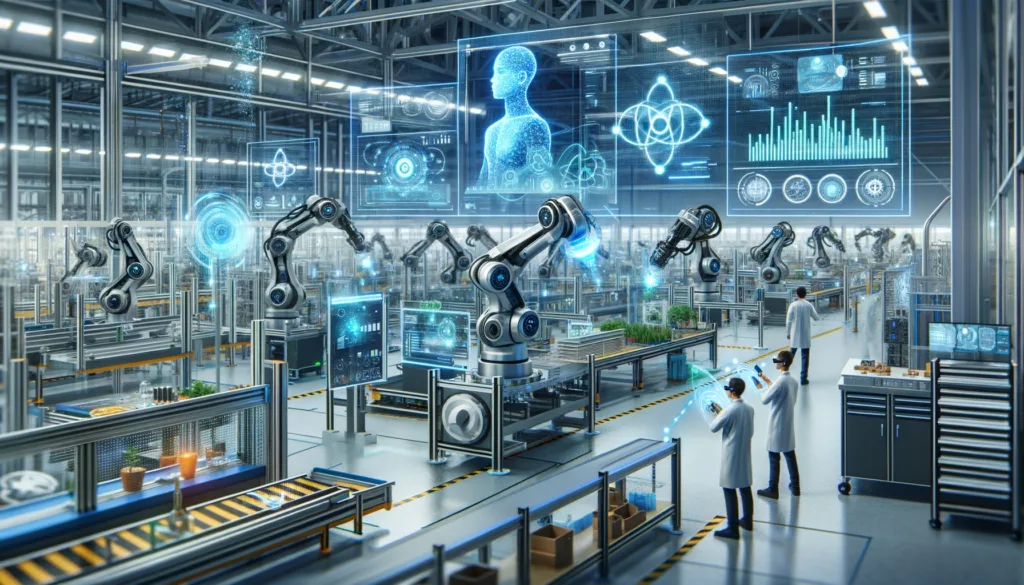
Integrating IoT and Digital Twins in Industrial Automation
IoT sensors play a vital role in feeding data into digital twins, enabling accurate real-time representation of assets and processes.
Real-Time Data Collection and Analysis
IoT sensors continuously collect data on various parameters such as temperature, vibration, and pressure. This data is then used by digital twins to monitor conditions and predict failures, creating a more resilient and adaptable automation environment.
- Example: In a factory, IoT-enabled digital twins can analyze temperature fluctuations in machinery, alerting operators to potential overheating issues before they lead to equipment failure.
Enhanced Connectivity and Remote Monitoring
IoT-connected digital twins allow for remote monitoring and control, enabling operators to manage assets across multiple sites from a centralized location.
- Example: Energy companies monitor remote wind turbines through digital twins, allowing for real-time oversight without the need for on-site personnel.
Challenges and Limitations of Digital Twins
The implementation of digital twins in industrial automation offers vast potential, yet it is not devoid of challenges and limitations that must be addressed. One significant concern surrounds data security. As digital twins rely heavily on real-time data analysis and cloud computing, the possibility of cyber attacks becomes a pressing issue. Sensitive operational data, if compromised, could lead to considerable financial losses and operational disruptions. Ensuring robust cybersecurity measures are in place is therefore a critical factor in the successful deployment of any digital twin system.
Moreover, the successful operation of digital twins requires a skilled workforce. The need for personnel proficient in data analytics, modeling, and IoT technologies has increased. This shortage of skill can hinder the effective implementation and maintenance of digital twins, as organizations may struggle to find qualified applicants capable of handling this sophisticated technology. Consequently, investing in training and development for existing employees is necessary, which can involve considerable time and resources.
Integration with existing systems also presents challenges. Industries often rely on legacy systems that may not be compatible with modern digital twin technologies. The effort and cost associated with integrating these systems, or transitioning to new ones, can be significant. Organizations must evaluate existing infrastructure, which may necessitate refurbishing or replacing outdated equipment to harness the full potential of digital twins.
Additionally, the financial investment required for setting up a comprehensive digital twin infrastructure can be daunting. Costs involve not only the technology itself but also training, maintenance, and ongoing operational expenses. Businesses must conduct thorough cost-benefit analyses to ascertain whether the advantages of implementing digital twins outweigh these initial and long-term outlays.
Despite the benefits, implementing digital twins in industrial automation presents challenges, including:
High Initial Investment Costs
Digital twin technology involves significant setup costs for sensors, data infrastructure, and software, which may deter smaller companies.
Data Management and Integration
Integrating data from various sources and managing massive data volumes can be complex and may require specialized data processing and storage capabilities.
Cybersecurity Risks
As digital twins rely on IoT connectivity and cloud services, they can be vulnerable to cyberattacks. Protecting data and infrastructure is critical to ensure system security and operational reliability.
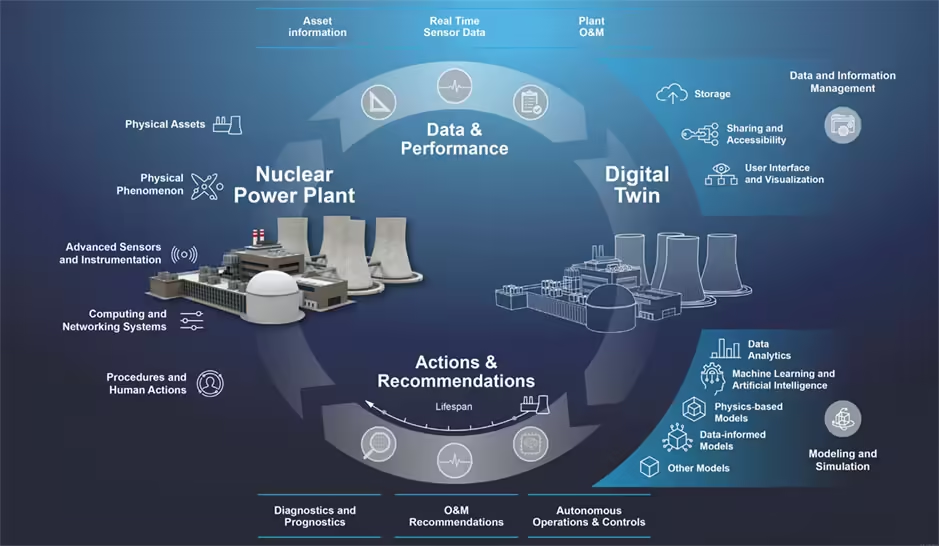
The Future of Digital Twins in Industrial Automation
The concept of digital twins is poised to undergo significant evolution, driven by advancements in technology and an increasing reliance on data. As industries continue to embrace digitalization, the future of digital twins in industrial automation appears promising. These digital replicas or simulations of physical assets are already enhancing operational efficiencies and enabling predictive maintenance, but the integration of artificial intelligence (AI) and machine learning is set to take their capabilities to new heights.
In the near future, we expect digital twins to become increasingly sophisticated, allowing for real-time data processing and analysis. This will enhance decision-making processes by providing deeper insights into system performance and operational workflows. AI algorithms will be utilized to analyze the vast amounts of data collected from physical assets, enabling the digital twin to simulate various scenarios and predict outcomes. As a result, industries can achieve higher levels of efficiency and reliability in their operations.
Moreover, the incorporation of machine learning within digital twin applications will facilitate continuous improvement. These systems will not only provide insights based on historical data but will also learn from new information, adapting their performance predictions and recommendations accordingly. This adaptive nature is expected to reduce downtime and optimize resource utilization significantly.
Another key trend is the increasing connectivity and interoperability among different digital twin systems. As industries adopt the Internet of Things (IoT), digital twins will become more integrated within smart factory environments, enabling seamless interactions between various machines and systems. This interconnectedness will drive innovations in automation, allowing for enhanced coordination and collaboration.
As we look ahead, it is clear that digital twins will play a vital role in shaping the future of industrial automation, with their potential being unlocked further through advancements in AI, machine learning, and interconnected technologies. These developments will pave the way for more efficient and responsive industrial ecosystems.
Case Studies: Success Stories
In the realm of industrial automation, several companies have turned to digital twin technology to address their unique challenges and enhance operational efficiency. One notable example is Siemens, which implemented digital twins in their manufacturing processes. Faced with a high level of production complexity and the need for real-time monitoring, Siemens developed a comprehensive digital twin of their production line. This solution allowed them to simulate production environments, test new configurations, and predict equipment failures before they occurred. As a result, Siemens reported a 30% reduction in downtime, leading to significant cost savings and improved productivity.
Another compelling case study is that of General Electric (GE), which adopted digital twins within their aviation sector. GE faced challenges related to engine performance optimization and predictive maintenance. By creating a digital twin for each engine, they could analyze data from thousands of flights in real-time. This approach enabled them to identify operational anomalies and make informed recommendations to airlines regarding maintenance schedules. The outcome was a remarkable 15% improvement in engine efficiency, which not only reduced operational costs for their customers but also contributed to enhanced safety standards across the industry.
Ford Motor Company is also leveraging digital twins to revolutionize automotive manufacturing. The company encountered obstacles in its supply chain management and production workflow. By implementing digital twin technology to model their supply networks, Ford was able to visualize and analyze the impact of potential disruptions. This proactive approach allowed them to optimize inventory levels and reduce lead times significantly. They reported a 20% increase in overall supply chain efficiency as a direct outcome of their digital twin applications. These case studies exemplify how digital twins are not merely theoretical but are actively transforming industries by solving real challenges and delivering quantifiable benefits.
Conclusion: The Transformative Power of Digital Twins
In recent years, digital twins have emerged as a revolutionary technology, fundamentally altering the landscape of industrial automation. This innovative approach allows for the creation of virtual representations of physical assets, enabling organizations to monitor, analyze, and optimize their operations in real time. The insights gained from these digital replicas can lead to significant improvements in efficiency, productivity, and decision-making processes.
The transformative power of digital twins is evident in various industrial sectors, ranging from manufacturing to supply chain management. For instance, in manufacturing, digital twins enhance predictive maintenance strategies by simulating machine performance and predicting failures before they occur. This proactive approach not only minimizes downtime but also extends the lifespan of equipment. Similarly, in supply chain management, digital twins provide insights into inventory levels, logistics, and demand forecasting, allowing businesses to adapt quickly to market changes.
Moreover, the integration of digital twins with advanced technologies such as the Internet of Things (IoT), artificial intelligence (AI), and machine learning further amplifies their capabilities. By harnessing real-time data from IoT devices, organizations can create more accurate and dynamic models of their assets. Meanwhile, AI and machine learning algorithms can analyze this data to uncover patterns and trends, driving continuous improvement and innovation in processes.
As industries continue to evolve, the adoption of digital twins will undoubtedly play a critical role in shaping the future of industrial automation. Organizations that embrace this technology stand to gain a competitive edge, enhancing not only their operational effectiveness but also their ability to respond to customers’ needs. Therefore, it is essential for businesses to explore the possibilities offered by digital twins and consider integrating this game-changing technology into their strategies for sustainable success.