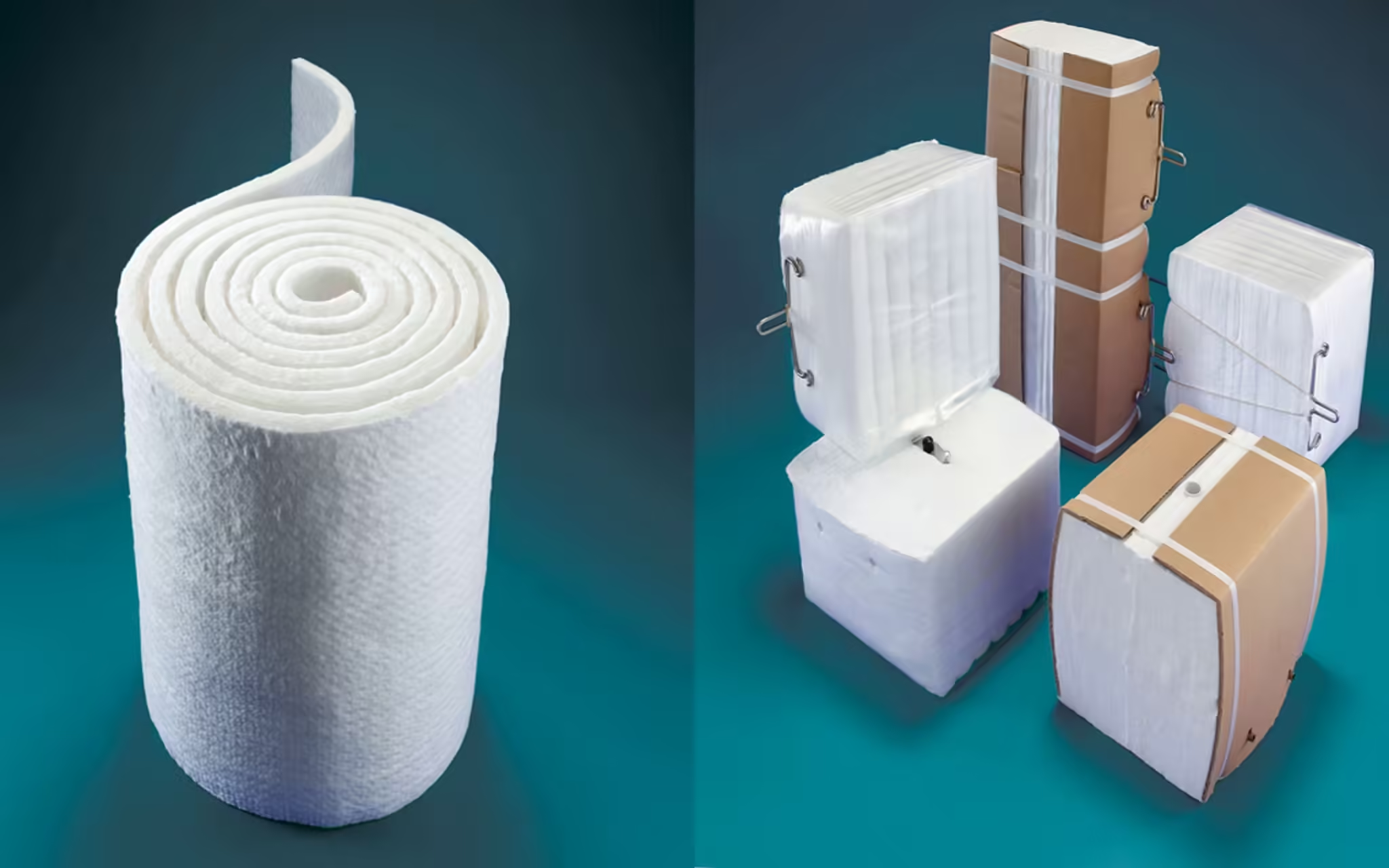
Introduction to High-Temperature Insulation Materials
High-temperature insulation materials play a critical role in a variety of industrial applications, particularly those that involve extreme thermal environments. These materials are essential in ensuring energy efficiency, safety, and operational effectiveness in sectors such as manufacturing, aerospace, and metallurgy. Among the most widely used high-temperature insulation materials are Refractory Ceramic Fiber (RCF) and Alkaline Earth Silicate Wool (AESW). Both options provide effective insulation but have distinct properties, which merits a thorough comparison.
Refractory Ceramic Fiber is known for its exceptional thermal performance and lightweight structure, making it a popular choice in applications requiring high resistance to heat. RCF can handle temperatures exceeding 1,600 degrees Celsius (2,912 degrees Fahrenheit), providing effective thermal insulation in furnaces, kilns, and other high-temperature systems. Its inherent flexibility allows for easy installation and adaptation to various shapes and sizes, additionally contributing to its widespread use across multiple industries.
On the other hand, Alkaline Earth Silicate Wool is gaining recognition due to its lower bio-solubility compared to traditional insulation materials. This characteristic, along with its thermal stability and chemical resistance, makes AESW a favorable option for many industrial applications. It is commonly applied in boiler systems, power generation, and petrochemical processes. As industries increasingly prioritize safety and environmental considerations, the demand for AESW has risen, highlighting its significance in modern insulation strategies.
In comparing RCF and AESW, it is crucial to consider various criteria, including thermal performance, chemical resistance, and market demand. This analysis will help in understanding the advantages and limitations of both types of high-temperature insulation materials, providing valuable insights for businesses and professionals in the field.
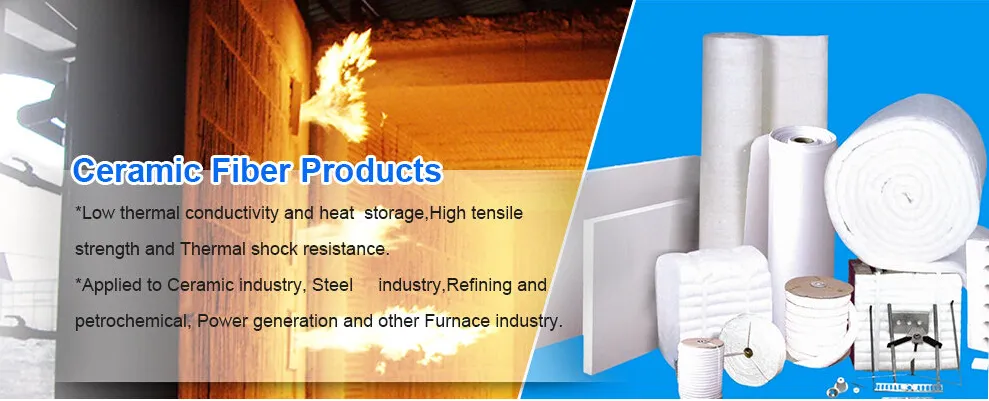
Properties of Refractory Ceramic Fiber
Refractory Ceramic Fiber (RCF) is renowned for its exceptional thermal properties, making it suitable for a variety of high-temperature applications. A primary characteristic of RCF is its low thermal conductivity, which ranges typically from 0.08 to 0.14 W/m·K. This quality ensures efficient insulation, preventing heat loss and maintaining elevated temperatures in industrial processes. Moreover, RCF can withstand extreme temperatures, often exceeding 1,200 degrees Celsius (2,192 degrees Fahrenheit), without compromising its structural integrity.
Another notable feature of RCF is its superior resistance to chemical degradation. Unlike many insulating materials, RCF remains stable and functional in the presence of various chemicals and contaminants, including oils, solvents, and acidic environments. This resilience ensures longevity and reliability in applications such as furnace linings and kilns, where exposure to harsh substances is common.
Durability is another key aspect of RCF, as it is engineered to withstand mechanical stresses, thermal shock, and aging. This enhanced durability makes RCF a cost-effective choice in industrial settings, reducing the need for frequent replacements. The manufacturing process of RCF typically involves the use of aluminosilicate fibers, produced through a spinning method that aids in achieving a lightweight yet robust product. The fiber composition, predominantly consisting of alumina and silica, contributes significantly to the material’s heat resistance and structural properties.
The unique properties of RCF position it as a preferred material in various industries, including aerospace, automotive, and energy production. Its ability to maintain performance under extreme conditions while offering significant insulation makes it an integral component where thermal management is critical. With the continuous evolution of materials science, RCF continues to adapt, providing innovative solutions for modern high-temperature applications.
Refractory Ceramic Fiber, also known as Aluminosilicate Wool (ASW), is a fibrous material made from molten silica (SiO2) and alumina (Al2O3) mixed with other materials. It is classified as a man-made vitreous fiber (MMVF). RCFs are used extensively in industrial furnaces, kilns, and other high-temperature environments because of their ability to resist temperatures as high as 1400°C (2552°F).
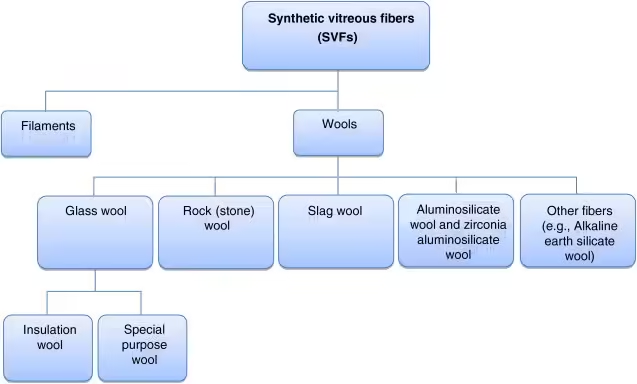
Key Properties of RCF:
- Thermal Stability: High resistance to heat and thermal shock.
- Low Thermal Conductivity: Provides superior insulation even at elevated temperatures.
- High Mechanical Strength: Excellent resilience under mechanical stresses.
- Lightweight: Lower weight than many traditional insulation materials, making it easy to handle and install.
- Versatility: RCF can be shaped into different forms, including blankets, boards, and modules.
Limitations:
- Health Concerns: RCF has been classified as a Category 2 carcinogen under the European Union’s REACH regulation due to its fibrous nature and the potential for causing respiratory issues, including lung fibrosis and mesothelioma.
- Environmental Impact: The production of RCF generates waste and emissions that can be harmful to the environment.
Major Applications:
- Petrochemical Industry: Furnace linings, heater insulation, and reformer insulation.
- Metallurgical Industry: Used in blast furnaces and ladles.
- Ceramics and Glass Industry: For kiln linings and insulation for glass manufacturing.
Properties of Alkaline Earth Silicate Wool
Alkaline Earth Silicate Wool (AESW) is a highly engineered insulation material known for its impressive thermal and acoustic properties. Composed primarily of silica, alumina, and various alkaline earth oxides, this material delivers exceptional thermal performance, making it suitable for a wide range of applications in industrial and commercial settings. Its unique composition allows it to withstand high temperatures, typically ranging from 1,000°C to 1,200°C, without compromising its structural integrity. This remarkable thermal resistance is complemented by its low thermal conductivity, a critical feature that enhances energy efficiency in buildings and processes.
Another defining aspect of AESW is its acoustic insulation capabilities. The fibrous structure of the material effectively traps sound waves, reducing noise transmission in adjacent environments. This property makes AESW an ideal choice for applications where sound attenuation is essential, such as in construction, transportation, and industrial noise control. By integrating Alkaline Earth Silicate Wool into architectural designs, builders can create quieter, more comfortable spaces without sacrificing thermal protection.
Furthermore, the performance of AESW under extreme conditions is noteworthy. It exhibits excellent resistance to chemical and mechanical degradation, allowing it to maintain its insulation properties even when exposed to harsh environments. This resilience is particularly valuable in applications involving corrosive substances or extreme temperature fluctuations. The manufacturing process of AESW employs specialized techniques to enhance its durability while keeping the fibers lightweight, which facilitates easy handling and installation.
In summary, Alkaline Earth Silicate Wool emerges as a versatile insulation option distinguished by its thermal and acoustic properties, along with robust performance under extreme conditions. Its innovative composition positions it favorably in the insulation market, appealing to a variety of industries seeking dependable and effective solutions for heat and sound management.
Alkaline Earth Silicate Wool (AES), also known as bio-soluble fiber, is a high-temperature insulation material made from silica (SiO2) and calcium-magnesium compounds. AES wool was developed as a safer alternative to RCF, offering similar thermal properties but with a lower health risk. It is classified as biodegradable, meaning that when inhaled, the fibers break down in the body, posing less of a long-term health risk compared to RCF.
Key Properties of AES:
- Lower Health Risk: AES fibers are considered bio-soluble, meaning they dissolve in bodily fluids and are less likely to cause long-term respiratory issues.
- Thermal Resistance: Can withstand temperatures up to 1200°C (2192°F), which makes it suitable for many industrial applications.
- Chemical Stability: Excellent resistance to acids and other corrosive environments.
- Lightweight and Flexible: Similar to RCF in terms of weight and ease of installation.
- Sustainability: More environmentally friendly due to the reduced health risks and compliance with modern safety regulations.
Limitations:
- Lower Temperature Resistance: Compared to RCF, AES wool has a slightly lower maximum temperature resistance, which limits its use in ultra-high-temperature applications.
- Cost: In some markets, AES wool can be more expensive than RCF, particularly in regions where manufacturing costs are higher.
Major Applications:
- Power Generation: AES wool is used in boilers and turbines, particularly in systems where high-temperature insulation is needed without compromising worker safety.
- Automotive Industry: Exhaust insulation, especially in diesel engines, where high temperatures are common.
- Fire Protection: AES is frequently used in passive fire protection systems due to its stability at high temperatures.
Technical Performance Comparison
Thermal Insulation
Both RCF and AES offer excellent thermal insulation properties, but RCF generally performs better at higher temperatures due to its composition. RCF fibers can withstand temperatures up to 1400°C, while AES fibers degrade beyond 1200°C.
However, for applications where the temperature is below 1200°C, AES can perform just as well as RCF. In fact, AES often provides better insulation at mid-range temperatures (800-1200°C) due to its lower thermal conductivity.
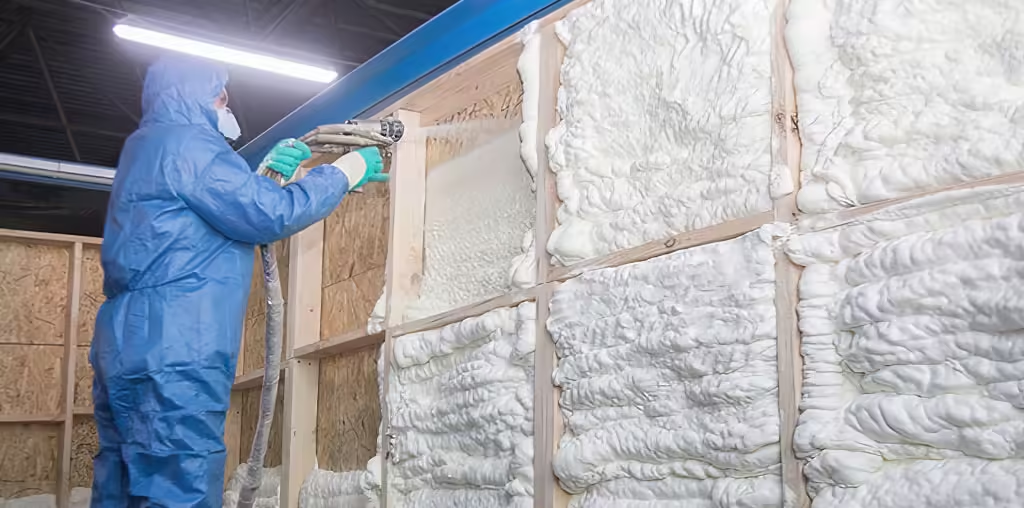
Chemical Resistance
AES fibers demonstrate superior resistance to chemical attack, particularly from acidic environments. This makes AES ideal for use in industries where acidic gases or chemicals are present, such as flue gas treatments in power plants.
On the other hand, RCF has excellent resistance to most chemical environments but can be degraded in the presence of certain alkalis, making it less suitable for highly alkaline environments.
Mechanical Properties
Both RCF and AES wool are lightweight and have good mechanical strength. However, RCF tends to be slightly more robust at very high temperatures, where AES may experience fiber degradation over time. RCF is also more resistant to mechanical wear and tear in furnace linings and other applications where high mechanical stresses are common.
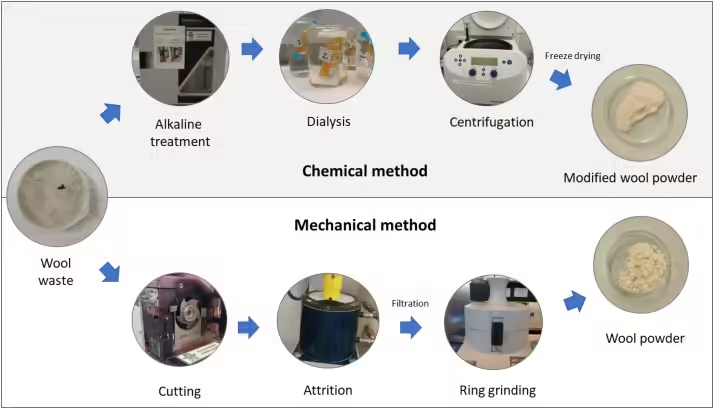
Durability and Longevity
RCF has been the go-to material in industrial settings for decades because of its proven durability and ability to maintain performance over long periods. AES is a newer material and, while it is designed to be durable, may not match the long-term performance of RCF in ultra-high-temperature settings.
However, AES does have an advantage in situations where frequent maintenance is required because it is safer to handle and poses less risk to workers during installation or replacement.
Market Demand and Applications
The market demand for Refractory Ceramic Fiber (RCF) and Alkaline Earth Silicate Wool (AESW) is influenced by various industrial applications, each benefiting from the unique properties of these materials. RCF is widely utilized in sectors such as aerospace, automotive, and manufacturing due to its excellent thermal insulation characteristics and high-temperature resistance. The aerospace industry, specifically, relies heavily on RCF for its lightweight thermal insulation in engine components, heat shields, and high-value thermodynamic applications. As the aerospace sector continues to evolve, RCF’s demand is anticipated to grow further, driven by advancements in aircraft design and manufacturing.
In the automotive industry, the demand for thermal insulation materials, including RCF, is increasing, particularly with the emphasis on energy efficiency and performance in vehicle design. The shift towards electric vehicles necessitates improved insulation properties to manage thermal stages during operation, thus fostering a favorable market outlook for RCF. Simultaneously, AESW is gaining traction in construction applications due to its non-carcinogenic nature and environmental advantages. As stringent regulations regarding occupational health take center stage, AESW is becoming the preferred choice in building materials, offering comparable thermal properties with improved safety profiles.
Furthermore, the manufacturing sector continues to experience a need for high-temperature resistance materials, which bolsters the market demand for both RCF and AESW. Emerging applications, particularly in energy production sectors such as renewable energy installations and power generation facilities, are likely to contribute to growth forecasts for these materials. Increased investments in infrastructure and energy projects worldwide underscore the vital role that refractory materials play in sustainability efforts. Overall, the demand dynamics for RCF and AESW suggest a robust market landscape, responsive to evolving industry needs and regulatory frameworks.

Environmental and Health Considerations
When evaluating the environmental and health aspects of Refractory Ceramic Fiber (RCF) and Alkaline Earth Silicate Wool (AESW), it is essential to recognize the differing regulations and safety implications associated with these materials. RCF, composed primarily of alumina and silica, has been classified as a possible human carcinogen by agencies such as the International Agency for Research on Cancer (IARC) due to its fibrous nature. As a result, stringent workplace exposure limits have been established to minimize any risks associated with inhalation or dermal contact. Proper safety measures, including personal protective equipment (PPE) and effective ventilation systems, are crucial in mitigating potential health hazards when handling RCF.
In contrast, AESW is often manufactured from a sequence of naturally occurring silicate minerals, and it has gained recognition as a safer alternative to RCF. Although further research is necessary to solidify its safety profile, current studies suggest that AESW presents lower health risks, making it a preferable choice for applications where exposure can occur. Regulatory frameworks governing AESW are generally less stringent compared to those for RCF, indicating a more favorable alignment with contemporary health and safety standards.
The end-of-life management of these materials also varies significantly. RCF faces challenges in recycling due to its composition, which necessitates specific disposal strategies to adhere to environmental regulations. Conversely, AESW is often regarded as more sustainable, with potential for recycling and repurposing in various industrial applications. This circular economy approach not only reduces waste but also lessens the environmental footprint associated with disposal. Overall, the choice between RCF and AESW involves a careful assessment of health risks, regulatory compliance, and sustainable disposal practices, which are vital for informed decision-making in material selection.
Cost Analysis of RCF vs. AESW
The cost of Refractory Ceramic Fiber (RCF) and Alkaline Earth Silicate Wool (AESW) is influenced by multiple factors including raw material expenses, manufacturing methods, and market dynamics. In analyzing these costs, it is important to first consider the raw materials utilized in each type of fiber. RCF is primarily derived from alumina-silica compounds, which can be subject to volatility in the mineral markets, while AESW is produced from silicate materials that might have different price fluctuations tied to their sources and availability.
Manufacturing costs also play a critical role in determining the final price of these materials. The processes employed for producing RCF tend to be more energy-intensive and require more sophisticated technology due to the high-temperature conditions involved. In contrast, AESW production generally mandates less energy input, which can translate to lower manufacturing costs. Consequently, when comparing RCF and AESW, the production methods can substantially affect price points.
Furthermore, market fluctuations impact the cost of both materials. Changes in demand for insulation solutions, driven by shifts in industries such as aerospace, automotive, and construction, can directly affect market pricing. It’s notable that during periods of heightened demand, the cost of RCF may rise more sharply than that of AESW due to its niche applications and specialized manufacturing techniques.
When evaluating the correlation between cost and performance characteristics, RCF typically exhibits superior thermal resistance and durability but at a higher price point. Conversely, AESW is often regarded as a cost-effective alternative with commendable thermal insulation capabilities, though it may not match RCF in extreme temperature applications. Thus, understanding the cost dynamics of RCF and AESW is essential for making informed decisions regarding material selection based on specific practical applications.
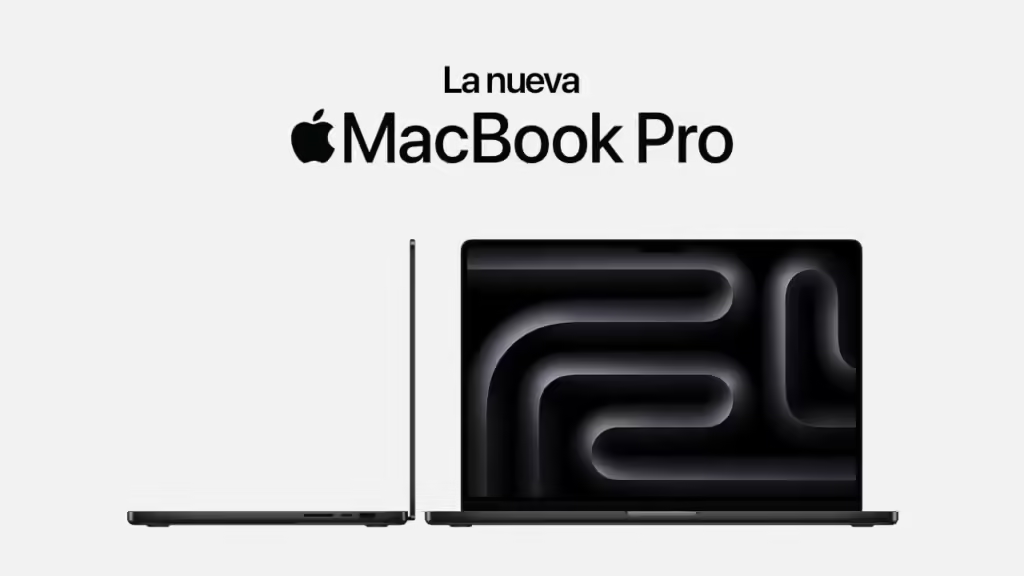
Technological Innovations in Fiber Materials
Recent advancements in fiber materials, particularly within the domains of Refractory Ceramic Fiber (RCF) and Alkaline Earth Silicate Wool (AESW), are increasingly shaping industry standards and consumer preferences. These innovations span various facets of production, material properties, and safety enhancements, thereby playing a vital role in the evolution of environmental and industrial applications.
One significant innovation is the advancement in manufacturing processes, which has directly contributed to the efficiency and cost-effectiveness of fiber materials. The incorporation of modern techniques, such as advanced spinning technologies and automated quality control measures, has led to the consistent production of high-quality RCF and AESW. These methods not only streamline operations but also reduce waste, aligning with the growing emphasis on sustainability within the industry.
Moreover, improvements in material properties have become a focal point of research and development. For instance, AESW has seen enhancements in thermal stability and resilience, making it a more favorable alternative to traditional fiber materials in specific applications. Similarly, RCF has benefitted from innovations aimed at enhancing its thermal conductivity and mechanical strength, which extends its service life and reliability under extreme conditions. These advancements are critical as industries seek materials that can withstand more demanding operational environments while maintaining safety protocols.
The impact of such innovations on market trends cannot be overstated. As manufacturers prioritize safety and material performance, consumer preferences are shifting towards products that embody these advancements. The growing demand for versatile, high-performance insulation solutions has consequently fostered a competitive market landscape. This evolution highlights the importance of continuous research and development efforts in driving the future success of both RCF and AESW applications.
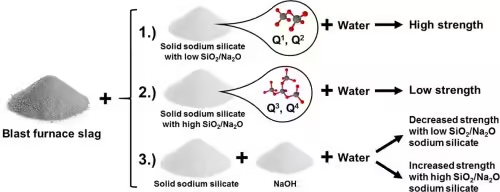
Expert Opinions and Case Studies
In the evaluation of refractory materials, particularly Refractory Ceramic Fiber (RCF) and Alkaline Earth Silicate Wool (AESW), expert insights play a crucial role in understanding their distinct advantages and limitations. Industry specialists note that RCF exhibits exceptional thermal resistance and lower thermal conductivity, making it a preferred choice in high-heat industries such as steel manufacturing and furnace construction. Experts cite that RCF’s flexibility allows for easy installation in complex geometries, providing an effective solution for thermal insulation in various applications.
Conversely, AESW is celebrated for its environmentally friendly composition, devoid of crystalline silica, making it a safer alternative for workers involved in installation and maintenance. Experts highlight AESW’s robust performance in high-temperature settings, particularly in sectors related to energy generation, where long-term durability is vital. A case study from a power plant demonstrated that replacing RCF with AESW resulted in not only enhanced safety but also significant reductions in maintenance costs due to lower wear and tear over operating cycles.
Case studies further reinforce the notion that while both materials serve critical roles in heat management, their application can vary significantly based on operational context. For instance, a manufacturer in the aerospace industry reported that RCF was essential in meeting stringent temperature control requirements, whereas AESW was effectively utilized in areas where exposure to moisture was a significant consideration. These insights reflect that the choice between RCF and AESW often hinges on specific industry needs, operational conditions, and regulatory requirements, highlighting the importance of a tailored approach in material selection.
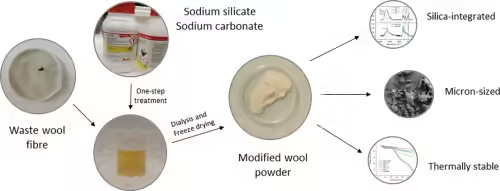
Conclusion and Future Trends
In conclusion, the comprehensive comparison of Refractory Ceramic Fiber (RCF) and Alkaline Earth Silicate Wool (AESW) reveals critical insights regarding their respective properties, market dynamics, and applications in high-temperature insulation. RCF has established itself as a widely used material, celebrated for its thermal stability and performance in extreme conditions. However, concerns regarding its potential health impacts due to fibrous composition have led to increased scrutiny and regulatory pressures. On the other hand, AESW emerges as a promising alternative, characterized by its enhanced safety profile and lower environmental impact, appealing to industries aiming to comply with stringent regulations.
Looking ahead, the market for insulation materials is expected to evolve significantly. Regulatory changes aimed at reducing the use of hazardous materials may drive a shift in demand from RCF towards AESW. Manufacturers are likely to invest in research and development to enhance the properties and applications of AESW, making it more competitive in various industrial sectors. Furthermore, the growing emphasis on workplace safety and environmental sustainability will play a crucial role in shaping the preferences of end-users.
Technological advancements, particularly in the manufacturing processes of both materials, are anticipated to influence market dynamics. Innovations aimed at improving the performance of AESW could lead to its increased adoption in areas traditionally dominated by RCF. Moreover, the growing demand for energy-efficient and sustainable solutions in the construction, automotive, and aerospace industries may further accelerate the transition towards alternative insulation materials.
Overall, while RCF continues to hold a vital place in high-temperature insulation applications, the potential for AESW to carve out a larger market share presents exciting opportunities for manufacturers and users alike. The industry landscape will likely be shaped by these factors in the coming years, ushering in a new era of insulation solutions.